Description
Key Features and Benefits
- Non-intrusive inspection—Sensors simply bond or are clamped onto the inspection area
- Remote locations—Offshore platforms (manned and unmanned), remote pipeline sites or inaccessible areas
- No scaffolding or rigging costs—Once installed no need to revisit the site (fit & forget)
- Early warning systems—Software provides trending, warning and alarm information with data on demand
- Accuracy—Measurement repeatability to 0.2 mm (0.008”) (low temp) or 0.0025 mm (0.0001”) (high temp)
- Operator safety—Eliminates the need to send operators into hazardous environments or remote locations to carry out wall thickness monitoring
- Increased asset integrity—The application of monitoring techniques can easily be justified when you consider the consequences of internal wall loss:
- Improved outage planning
- Minimize unscheduled shutdowns
- Eliminate hazard to personnel
- Reduce probability of environmental issues
- Enhanced API-RBI protocols
Importance of Wall Thickness Monitoring
The negative effects of corrosion and erosion cost industry billions of dollars every year in unscheduled plant or pipeline shutdowns, lost production, high repair costs or imposed fines. Experts state that 20 to 25% of corrosion-related costs could be avoided. Corrosion and erosion data monitoring technologies are an important first step toward realizing those savings.
GE offers a practical, cost-effective and direct approach. Our Rightrax ultrasonic wall thickness measuring and monitoring systems provide continuous real-time data on the remaining wall-thickness of a pipe, vessel or other critical plant component.
Maximum Uptime, Minimum Inspection Costs
GE’s Rightrax systems are changing the way that critical remaining wall thickness data is measured and managed. This breakthrough technology helps increase safety and productivity while reducing overall inspection costs.
The Rightrax system uses permanently-installed ultrasonic sensors that permit remote monitoring of critical, restricted or high-temperature areas up to 350°C. Once fitted, the system provides online remote access to data, eliminating the need to erect scaffolding, remove insulation or shut down plants. Online monitoring also reduces costly and labor-intensive planned maintenance schedules and traditional inspection routines.
More Than Wall Thickness Measurement
- Provide accurate feedback to manage opportunity crude processing in a refinery by monitoring effects on pipe wall thicknesses
- Drive down probability of failure with data on demand/data on PCs
- Provide reliable and highly repeatable data that can be used to drive maintenance planning activities to save cost on unexpected material orders and spare inventory
- Provide support for chemical injection programs by supplying accurate and reliable pipe wall thickness data
- Interface with plant asset management systems, such as System 1, viewing fixed and rotating asset conditions in a single system
- Real-time, highly accurate thickness data
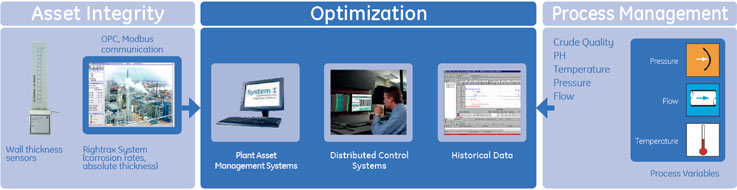
Applications
- High temperature crude lines
- Difficult-to-access or remote high temperature locations
- High temperature pressure vessels
Specifications
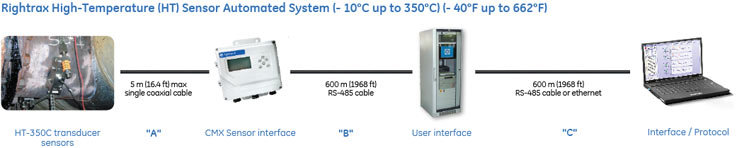
Hazardous area rating | Intrinsically safe |
---|---|
Transducer type | Single-element delay-line sensor |
Transducer frequency and diameter | 5 MHz x single point |
Max number of transducers / system | 128 tranducers |
Transducer temperature range min/ max | -40˚ C to 350˚ C (-40˚ F to 662˚ F) |
Operational measurement range (min/max) | 3 mm – 17 mm (0.118 in – 0.669 in) |
Resolution / accuracy | +/- 0.0025 mm (+/- 9.8×10-5 in) |
Maximum cable distance “A” | 5 m (16.4 feet) |
Maximum cable distance “B” | 600 m (1968 ft) (RS-485) |
Maximum cable distance “C” | 600 m (1968 ft) (RS-485 or ethernet) |
Interface / protocol | MODBUS SCADA System 1 OPC 3rd Party |